Robot Vision
2022-07-01
3534
分享海报
描述
在电动汽车所有的电子系统中,电池系统无疑是大家都密切关注的。电池系统包括可充电电池本身锂离子电池以及电池管理系统,也就是我们常说的BMS。BMS既要能够大幅度提高电池的使用率,也要对电池的安全性负责。
BMS中采集器与控制器是两大核心,目前采集器基本上都使用集成AFE,只有少数还在使用很早的分立元件采样电路。采集器里的重中之重就是AFE芯片,这一块国内起步较晚,基本被国外大厂所垄断,ADI、TI、NXP、松下、ST等等。
仅从AFE芯片本身的角度来看,各个不同AFE在外比较通道数量、面积、成本,在内比的是稳定性。在不同通道数量和采集性能(电压采集误差、速度、漏电流),每个芯片企业在模拟采集处理这里的差异还是挺大的。
合适的AFE——低噪高精度
首先我们需要的明确的是相对其他器件拥有广泛的选择来说,AFE可供选择的余地并不那么多,目前市面上主流国际大厂那些我们较为熟悉的AFE,内部结构可以说是大同小异,不同点更多集中在硬件资源方面以及针对功能安全要求设计的架构形式。
以ADI的LTC系列为例,为了实现卓越的准确度,系列采用了一个专用掩埋式齐纳电压基准,掩埋式齐纳电压基准随时间和工作条件变化,能实现以不到1.2mV的误差测量,稳定和准确兼顾。像LTC6811可测量多达12个串接电池的电压,不超过1.2mV的总测量误差。所有的12节电池可在不超过290μs内完成测量。

LTC6811,ADI
进一步看,如何在有噪声的情况下确保测量准确度?主流厂商的做法是通过ADC,但需要在降低噪声与转换速度之间进行权衡,也就是选择较低的数据采集速率来实现更高的噪声抑制。使用增量累加ADC多次采样,然后进行数字滤波。集成的低通滤波会消除作为测量误差源的噪声,确保前端在有噪声的情况下仍然确保测量准确度。
下面是主流BMS模拟前端厂商各系列主流型号在通道数以及测量总误差指标对比。
选择AFE时,首先关注的肯定是采集精度以及测量误差。采集精度是前提,剩下的不同主要在采样通道数量、内部ADC的数量、类型与架构上。如果再细一点,那就细节到温度点数量,功能安全需求等。除此之外,EMC是一个不可忽视的因素,在复杂的汽车射频环境下模拟前端的EMC也是很重要的一环。
BMS模拟前端:通信与可靠性
在车规应用上,往往会使用多种BMS监视拓扑来满足器件对准确性、可靠性、成本和功耗的需求。要知道为了在电动汽车/混合动力汽车的高EMI环境中支持分布式模块化拓扑,稳健的通信系统必不可少。
在TI经典的BQ系列模拟前端上,有多个GPIO/辅助输入可用于热敏电阻测量、驱动继电器、测量电压以及用作外围 SPI 器件的主SPI接口,还支持通过UART进行通信。此外,BQ系列模拟前端上隔离式差分菊花链通信接口允许主机通过单个接口与其他UIR监视器甚至电芯监视器进行通信。如果将菊花链通信接口配置为环形架构,主机在通信线路中断时能够与堆叠任一端的器件进行通信。
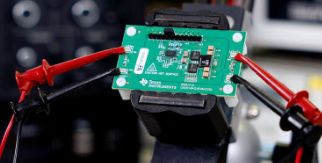
TI BMS模拟前端
NXP的MC3377系列BMS AFE同样支持标准SPI和变压器隔离菊花链与MCU进行通信,以实现数据处理和控制。通过变压器物理层以菊花链形式连接BJB是一个很有吸引力的办法。TPL接口专为BMS设计,能够支持高隔离电压,还有更高的电磁兼容性EMC特性以及更快的通信速度和同步测量,降低了与本地软件有关的复杂性。
NXP
ADI则通过创新的双线式isoSPI实现低功耗和高可靠性。为了提高可靠性,将isoSPI收发器连接到电池组的顶部,创建一个支持双向通信的环形拓扑,从而实现双通道高可靠性通信。isoSPI接口还提供了抗噪接口用于高电平RF信号,利用该接口可以将模块通过长电缆以菊花链形式连接,并以高达1 Mbps的数据速率运行。
在电池组这种充满电磁干扰挑战的环境里数据通信链路肯定要进行特别处理,以确保测量芯片与系统控制器之间稳健可靠的通信。
小结
不难看出,集成式BMS AFE在芯片层面解决了相当一部分的系统稳定性和功能安全的问题。目前主流的这些BMS模拟前端,从高精度到低噪声,从通信设计到系统稳健性都领先不少。车载应用上很难脱离这些芯片。毕竟在汽车恶劣的浪涌脉冲困难下,如果前端设计不好,后面的设计也无从谈起。
在上述这些主流AFE极度缺货的背景下,一些国产替代芯片获得了不少认可,下期我们来看看国内的高精度BMS模拟前端芯片。
打开APP阅读更多精彩内容