A new generation of devices is emerging that integrates temperature and humidity sensing alongside data converters and logic with sophisticated calibration. Integrating the sensor can reduce the complexity and reliability of the system and provide more protection for sensitive electronic designs, as demonstrated by the Si7005 from Silicon Labs.
Developments in CMOS process technology are opening up new opportunities for the designers of embedded systems. Adding low-K polymeric dielectrics into the design means capacitive humidity sensors can be built alongside integrated temperature sensors along with integrated heating elements. This combination provides a powerful way to reduce the size and complexity of a system.
However, this comes with new design considerations. While previous protection and calibration of the sensor was handled in a discrete part, now it is part of a more complex logic design. Although this has advantages for the calibration, it has challenges for the designers, especially for the new generation of devices that integrate both temperature and humidity sensors. There are also new ways for the parts to be specified, with the specification of the accuracy and measurement margins.
Designers now have to consider protection of the device during the reflow process, taking baking and hydrating of the device into account in the development of the system and how this impacts the accuracy of the sensor measurements both immediately and in the longer term.
The Si7005 from Silicon Labs offers an accurate, low-power, factory-calibrated digital solution for measuring temperature, humidity, and dew point in applications ranging from air conditioning and asset tracking to industrial and consumer platforms.
The monolithic CMOS digital relative humidity and temperature sensor integrates temperature and humidity sensor elements, an analog-to-digital converter, signal processing, calibration data, and an I2C host interface. The patented use of industry-standard, low-K polymeric dielectrics for sensing humidity enables the construction of a low-power, monolithic CMOS sensor with low drift and hysteresis, and excellent long-term stability.
Both the temperature and humidity sensors are factory-calibrated and the calibration data is stored in the on-chip non-volatile memory. This ensures that the sensors are fully interchangeable, with no recalibration or software changes required.
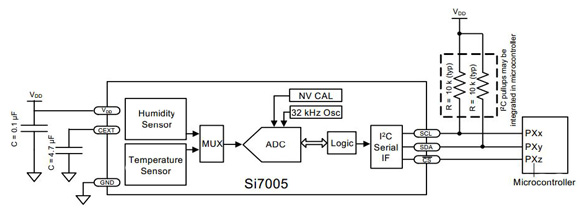
Figure 1: The Si7005 from Silicon Labs.
Environmental protection is a key consideration for applications that use a humidity and temperature sensor, so an optional factory-installed protective cover offers a low profile, convenient means of protecting the sensor during assembly (for example during reflow soldering), and throughout the life of the product, excluding hydrophobic or oleophobic liquids and particulates.
While the Si7005 is largely a conventional mixed-signal CMOS integrated circuit, relative humidity sensors in general, and those based on capacitive sensing using polymeric dielectric, have unique application and use requirements that are not common to conventional non-integrated devices. The main issues are the need to protect the sensor during board assembly, and the need to subsequently rehydrate the sensor. There is also the need to protect the sensor from damage or contamination during the product lifecycle, and designers have to consider the impact of prolonged exposure to extremes of temperature and/or humidity and their potential effect on sensor accuracy. This is coupled with the issues of calibration and the effects of humidity sensor ‘memory’, as well as the need to apply temperature correction and linearization to the humidity readings.
Relative humidity sensor accuracy
To determine the accuracy of a relative humidity sensor, it is placed in a temperature and humidity-controlled chamber. The temperature is set to a convenient fixed value (typically 30°C) and the relative humidity is swept from 20% to 80% and back to 20% in the following steps: 20% – 40% – 60% – 80% – 80% – 60% – 40% – 20%. At each set-point, the chamber is allowed to settle for a period of 30 minutes before a reading is taken from the sensor. Prior to the sweep, the device is allowed to stabilize to 50%RH. The RH accuracy is defined as the average of the two data points at each relative humidity set-point. In this case, the sensor shows an accuracy of 0.25%RH.
This provides an accuracy specification that includes unit-to-unit and lot-to-lot variation in non-linearity compensation, the accuracy of the factory calibration, and the margin for shifts that can occur during solder reflow (compensation for shift due to reflow is included in the linearization procedure below).
However, there are some limitations to the accuracy specification. It does not include hysteresis effects, which are typically ±1%, nor does it cover effects from long-term exposure to very humid conditions. Contamination of the sensor by particulates and chemicals can also have an effect. While the specification does not include variations due to temperature, once the temperature compensation is applied, the humidity readings will typically vary by less than ±0.05%/°C.
The capacitive relative humidity sensor in the Si7005 also needs linearization, and the accuracy specification applies after correction of non-linearity errors. The recommended linearization technique is to correct the measured relative humidity value with a second-order polynomial; the linear relative humidity (RH) value is calculated from the formula in Figure 2.

Figure 2: Linearization of the relative humidity value, where RHLinear is the corrected relative humidity value in %RH, RHValue is the uncorrected (measured) relative humidity value in %RH, and A2, A1, and A0 are unit-less correction coefficients derived through characterization of Si7005s by Silicon Labs; their values depend on whether compensation for a typical solder reflow is required.
The humidity sensor is calibrated at a temperature of 30°C as the sensor will give the most accurate relative humidity readings. For relative humidity measurements at other temperatures, the RH reading from the Si7005 must be compensated for the change in temperature relative to 30°C, using the values from the integrated temperature sensors. This makes the compensation process relatively simple and self-contained within the device.
Temperature compensated relative humidity readings can be calculated from the formula in Figure 3.

Figure 3: Temperature compensation for the Si7005, where RHTempCompensated is the temperature compensated relative humidity value in %RH and RHLinear is the linear corrected relative humidity value in %RH. Temperature is the ambient temperature in °C as measured by the Si7005 on-chip temperature sensor and Q1 and Q0 are unit-less correction coefficients derived through characterization of Si7005s by Silicon Labs. This temperature compensation is most accurate in the range of 15–50°C.
The Si7005 relative humidity sensor contains an integrated, resistive heating element that may be used to raise the temperature of the humidity sensor. This element can be used to drive off condensation or to implement dew point measurement when the Si7005 is used in conjunction with a separate temperature sensor such as another Si7005.
The heater can be activated by setting the D1 HEAT bit in the CONFIG register (register 0x03). Turning on the heater will reduce the tendency of the humidity sensor to accumulate an offset due to "memory" of sustained high humidity conditions. When the heater is enabled, the reading of the on-chip temperature sensor will be increased.
Hysteresis
The moisture absorbent film (polymeric dielectric) of the humidity sensor will carry a memory of its exposure history, particularly its recent or extreme exposure history. A sensor exposed to relatively low humidity will carry a negative offset relative to the factory calibration, and a sensor exposed to relatively high humidity will carry a positive offset relative to the factory calibration. This factor causes a hysteresis effect, the difference in %RH between the maximum absolute error on the decreasing humidity ramp and the maximum absolute error on the increasing humidity ramp at a single relative humidity set-point. This is expressed as a bipolar quantity relative to the average.
Prolonged exposure to high humidity will result in a gradual upward drift of the RH reading. The shift in sensor reading resulting from this drift will generally disappear slowly under normal ambient conditions. The amount of shift is proportional to the magnitude of relative humidity and the length of exposure. In the case of lengthy exposure to high humidity, some of the resulting shift may persist indefinitely under typical conditions. It is generally possible to substantially reverse this effect by baking the device.
Si7005 devices are shipped, like most ICs, vacuum-packed with an enclosed desiccant to avoid any drift during storage, as well as to prevent any moisture-related issues during solder reflow. Devices should be soldered using reflow and a ‘no clean’ solder process, as a water or solvent rinse after soldering will affect accuracy.
The measured humidity value will generally shift slightly after solder reflow. This shift is accounted for when using the linearization procedure given above. After soldering, the Si7005 should be allowed to equilibrate under controlled RH conditions (room temperature, 45–55%RH) for at least 48 hours to reach rated accuracy. During soldering, it is recommended that a protective cover of some kind be in place such as Kapton polyimide tape. Hot air rework is not recommended and soldering iron touch-up is possible if flux is not needed and care is taken to avoid excessive heating. If rework is required, the part can be removed by hot air and a new part soldered on by reflow.
Alternatively, Si7005s may be ordered with a factory fitted, solder-resistant protective cover which can be left in place for the lifetime of the product, preventing liquids, dust or other contaminants from coming into contact with the polymer sensor film.
Protecting the sensor
When the sensor operates on the principle of measuring a change in capacitance, any changes to the dielectric constant of the polymer film will be detected as a change in relative humidity. Therefore, it is important to minimize the probability of contaminants coming into contact with the sensor. Dust and other particles, as well as liquids can affect the RH reading. It is recommended that a filter cover be employed in the end system that blocks contaminants, but also allows water vapor to pass through. Depending on the needs of the application, this can be as simple as plastic or metallic gauze for basic protection against particulates, or something more sophisticated such as a hydrophobic membrane providing up to IP67 compliant protection.
As mentioned earlier, Si7005s may be ordered with a factory fitted, solder-resistant cover, which can be left in place for the lifetime of the product. It is very low profile, hydrophobic and oleophobic, and excludes particulates down to 0.35 microns in size. The sensor should also be protected from direct sunlight to prevent heating effects as well as possible material degradation.
After exposure to extremes of temperature and/or humidity for prolonged periods, the polymer sensor film can become either very dry or very wet; in each case the result is either high or low relative humidity readings. Under normal operating conditions, the induced error will diminish over time. From a very dry condition, such as after shipment and soldering, the error will diminish over a few days at typical controlled ambient conditions, for example, 48 hours of 45 ≤ %RH ≤ 55. However, from a very wet condition, recovery may take significantly longer. To accelerate recovery from a wet condition, a bake and hydrate cycle can be implemented. This operation consists of baking the sensor at 125°C for over 12 hours, followed by hydration at 30°C in 75%RH for 10 hours. Following this cycle, the sensor will return to normal operation in typical ambient conditions after a few days.
Long term drift/aging
Over long periods of time, the sensor readings may drift due to aging of the device. Standard accelerated life testing of the Si7005 has resulted in the specifications for long-term drift shown in Table 4 and Table 5 of the datasheet. This contribution to the overall sensor accuracy accounts only for the long-term aging of the device in an otherwise benign operating environment and does not include the effects of damage, contamination, or exposure to extreme environmental conditions.
Development support
A suite of hardware and software development tools for testing, characterization, prototyping, and software development is available to support the Si7005.
The Si7005USB-DONGLE Evaluation Kit comes with everything developers need to demonstrate and evaluate the Si7005. The board plugs into a PC via a USB socket and has a connector for adding the Si7005USB-EVB. This is a small daughter card that permits evaluation of the Si7005 at the end of a flex cable.
The Si7005EVB-UDP is a small daughter card for evaluating the Si7005 in conjunction with certain Unified Development Platform (UDP) components such as the C8051F960 Ultra-Low-Power Microcontroller Development Kit. It plugs directly into UDP MCU cards for fast prototyping and software development. Alongside the Si7005, there is also a connector for adding a Si7005-EVB via its flex cable, allowing the user to place the Si7005 in a temperature/humidity chamber or a product prototype.
The Si7005EVB-UDP-F960 Development Kit combines the C8051F960 Ultra-Low-Power Microcontroller Development Kit and the Si7005EVB-UDP daughter card with data-logger demonstration code. It is a complete package designed to support hardware and software development using the Si7005 and Silicon Labs’ ultra-low-power MCUs. It ships with example software that implements a portable, battery-powered data logger or asset tracker.
Figure 4: The development systems for the Si7005.
Conclusion
The development of new process technology has provided a highly-integrated device with temperature and humidity sensing, as well as heating elements controlled directly from the internal registers. This provides smaller, lower cost designs, but also means having to pay more attention to the manufacturing and long term stability of the system.